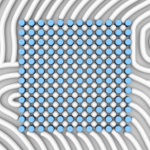
Una nueva técnica permite la producción de estructuras complejas de microchips en un paso de auto-ensamblaje.
David L. Chandler, MIT News Office. Original (en inglés).
Investigadores del MIT (Massachusetts Institute of Technology – Instituto Tecnológico de Massachusetts) han desarrollado un nuevo método para crear el complejo conjunto de cables y conexiones en microchips, utilizando un sistema de polímeros de auto-ensamblaje. El trabajo podría conducir eventualmente a una manera de hacer componentes más compactos en chips de memoria y otros dispositivos.
El nuevo método — desarrollado por el estudiante de doctorado visitante del MIT, Amir Tavakkoli, de la Universidad Nacional de Singapur, junto con otros dos estudiantes graduados y tres profesores en los departamentos de Ingeniería Eléctrica y Ciencias Computacionales (EECS) y de Ingeniería y Ciencia de los Materiales (DMSE) — es descrito en un artículo que será publicado este próximo mes de Agosto en la revista Advanced Materials; el artículo está disponible en línea ahora.
El proceso está estrechamente relacionado a un método que el mismo equipo describió el mes pasado en un artículo en Science, que hace posible la producción de configuraciones tridimensionales de cables y conexiones utilizando un sistema similar de polímeros autoensamblables.
En el nuevo artículo, los investigadores describen un sistema para producir matrices de cables que se encuentran en ángulos rectos, formando cuadrados y rectángulos. Si bien estas formas son la base para la mayoría de los diseños de circuitos de microchips, éstos son difíciles de producir a través del auto-ensamblado. Cuando las moléculas se auto-ensamblan, explica Caroline Ross, la profesora de Toyota de Ingeniería y Ciencia de los Materiales y co-autora de los artículos, tienen una tendencia natural a crear formas exagonales — como en un panal o en un conjunto de burbujas entre hojas de vidrio.
Por ejemplo, un conjunto de rodamientos pequeños en una caja “tiende a dar una simetría hexagonal, incluso aunque esté en una caja cuadrada”, Ross dice. “Pero eso no es lo que quieren los diseñadores de circuitos. Ellos quieren patrones con ángulos de 90 grados” — para superar la tendencia natural fue esencial producir un útil sistema de auto-ensamblaje, dice ella.
La solución del equipo crea una serie de pequeños postes en la superficie que guían los patrones de las moléculas de polímero de auto-ensamblaje. Esto resulta que tiene otras ventajas también: Además de producir patrones cuadrados y rectangulares perfectos de diminutos cables de polímeros, el sistema también permite la creación de una variedad de formas del material mismo, incluyendo cilindros, esferas, elipsoides y cilindros dobles. “Puedes generar este asombroso conjunto de características”, Ross dice, “con una plantilla muy simple”.
Karl Berggren, un profesor asociado de ingeniería eléctrica en el MIT y co-autor del artículo, explica que estas formas complejas son posibles porque “la plantilla, que está recubierta con el fin de repeler uno de los componentes poliméricos, causa una gran tensión local en el patrón. El polímero se tuerce y gira para tratar de evitar esta tensión, y al hacerlo se reorganiza en la superficie. Así podemos vencer las inclinaciones naturales de los polímeros, y hacer que creen patrones mucho más interesantes”.
Este sistema también puede producir características tales como conjuntos de agujeros en el material, cuyo espaciamiento está mucho más cerca de lo que se puede lograr utilizando métodos de fabricación de chips convencionales. Eso significa que puede producir características mucho más compactas en el chip de lo que los métodos actuales pueden crear — un paso importante en los esfuerzos en curso para empacar más y más componentes electrónicos en un determinado microchip.
“Esta nueva técnica puede producir múltiples [formas o patrones] simultáneamente”, dice Tavakkoli. Puede también hacer “patrones complejos, que es un objetivo para la fabricación de nanodispositivos”, con menos pasos que los procesos actuales. La fabricación de una amplia área de circuitos complejos en un chip utilizando la litografía por haz de electrones “podría tomar varios meses” dice. Por el contrario, utilizando el método de polímero auto-ensamblable tomaría sólo unos pocos días.
Eso está todavía demasiado lejos de la fabricación de un producto comercial, pero Ross explica grandes áreas en que este paso debe hacerse una sola vez para crear un patrón maestro, que luego pueda ser utilizado para estampar un revestimiento en otros chips en un proceso muy rápido de fabricación.
La técnica podría extenderse también más allá de la fabricación de microchips, dice Ross. Por ejemplo, un enfoque para la búsqueda de empacar cada vez mayores cantidades de datos en medios magnéticos como discos duros de computadoras, es utilizar un revestimiento magnético con un patrón muy fino estampado en él, definiendo con precisión las áreas donde cada bit de datos va a ser guardado. Un patrón tan fino podría potencialmente ser creado utilizando este método de auto-ensamblaje, ella dice, y luego estampado en los discos.
Craig Hawker, un profesor de química y bioquímica en la Universidad de California en Santa Barbara, que no estuvo involucrado en este trabajo, dice “Hay una necesidad y requisitos crecientes en la industria para encontrar una alternativa a la fotolitografía tradicional para la fabricación de dispositivos microelectrónicos de vanguardia. Este trabajo representa un logro fundamental en este campo y demuestra claramente que estructuras antes consideradas imposibles de alcanzar por una estrategia de auto-ensamblaje puede ahora ser preparada con un alto grado de fidelidad”.
Los colegas de Tavakkoli y Ross en este trabajo son los estudiantes de doctorado de DMSE, Adam Hannon y Kevin Gotrik, el profesor de DMSE, Alfredo Alexander-Kats y el profesor de EECS, Karl Berggren. La investigación, que incluye trabajo en el Laboratorio de Nanoestructuras y el centro de Litografía de Escaneo por Haz de Electrones del MIT, fue financiado por la Semiconductor Research Corporation, el Center on Functional Engineered Nano Architectonics, el Instituto Nacional de Recursos, la Alianza Singapore-MIT, la National Science Foundation, la Taiwan Semiconductor Manufacturing Company y Tokyo Electron.
Reimpreso con permiso de MIT News.
Fuente
http://web.mit.edu/ (en inglés)